金屬液在充填過程中由于金屬型壁摩擦阻力及型腔內氣體阻力因而使充填壓力、充填速度損耗增大,這是造成欠鑄、冷隔、花紋等鑄造缺陷的主要原因。同時薄壁件充填成型凝固時間短,如果壓鑄機的增壓起始時間和增壓速度調節性能欠佳或調節不當,壓射時,三級增壓效果就難于保證,勢必造成鑄件疏松,開裂薄壁鑄鋁件壓鑄成型是一個實現全面生產工藝技術管理的復雜過程,除正確選擇壓鑄機,保證模具設計制造質量、控制壓鑄工藝參數外,還涉及到工藝管理、壓鑄工操作水平等環節。
提高薄壁鋁件壓鑄優良品率的途徑
1正確選擇壓鑄機
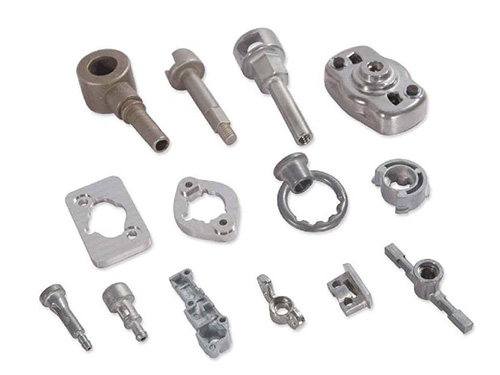
薄壁鋁件用的壓鑄機應是一種高性能的設備,其型號選擇除應滿足一般的原則外,還應盡量滿足下列一些條件:
(1)多泵供壓結構系統,以縮短工作壓力建壓和補壓時間;(2)多個貯能器,包括工作壓力貯能器、快壓射速度貯能器、增壓貯能器等,有高的快壓射速度,短的建壓時間和快的增壓速度;(3)建壓時間和增壓速度可調,建壓時間小于0.03s;(4)快壓射速度不小于7m/s,慢壓射行程不小于200mm,較高壓射比壓不小于140Mp。
2保證壓鑄模設計制造質量
設計薄壁鑄件壓鑄模時要特別注意下列幾個技術問題:
設計澆口系統時,應注意金屬液充填順暢,充填流程短為盒類鑄件,該類壓鑄鋁件采用側澆口或端面澆口成型均有困難,采用頂澆口較理想。面板類鑄件該件采用頂面環形澆口方案H比采用端面側澆口方案合理為圓筒類鑄件該件采用.處側澆口方案雖然充填流程短,但由于金屬液充填不暢,圓筒表面易產生旋渦等鑄造缺陷,而采用a或h方案均可保證獲得滿意的鑄件表面質量。
3其它工藝
(1)壓室內氣體占整個模具排氣量70%,因此盡量多排除壓室內氣體也是保證薄壁件成型重要因素,采用小的壓室直徑,保證壓室有足夠充滿度(較好大于50%),調節慢壓射行程(盡量長些),慢壓射速度(小于0.3m/s),增大模具排氣槽容量,合理增大沖頭與壓室間隙(保證單邊間隙0.05-0.07mm),及時清除沖頭上粘結的金屬、臟污等,以使排氣通暢。
(2)料餅(立式)或直澆口(臥式)厚度影響壓室充滿度及比壓傳遞,直澆口厚度小于5mm,鋁鑄件即出現嚴重的欠鑄、疏松等缺陷,直澆口厚度大于20mm,并進行定量勺料。
(3)熔煉合金時新舊料比大于7:3,并進行認真精煉處理。
(4)用壓鑄水基涂料,其涂料特點是模具溫度高的,涂料中水分和其他揮發物在壓鑄前就揮發了,減少了氣體含量,同時不易在鑄件表面產生油隔等缺陷。
薄壁鋁件壓鑄成型工藝一直是壓鑄工作者所關心的技術難題,我們經過多年的生產實踐積累了一些數據和經驗選擇高性能壓鑄機,設計制造高質量壓鑄模具,采用較高的內澆口充填速度,合適的模具溫度、合金澆入溫度及壓射比壓,嚴格其他的壓鑄工藝,薄壁鋁件壓鑄成型良品率達80%以上。
隨著高新技術產品的發展,使產品零件形狀向薄壁化、復雜化、大型化發展,薄壁鋁鑄件會更多,進一步開展對薄壁件壓鑄成型工藝的研究具有重要意義。
泊頭東固模具制造有限公司(http://www.hbdgmj.com)主營項目:壓鑄件流動性好,易熔焊,釬焊和塑性加工,在大氣中耐腐蝕,殘廢料便于回收和重熔;但蠕變強度低,易發生自然時效引起尺寸變化。鋁合金精密壓鑄零件加工變形的原因很多,與材質、零件形狀、生產條件等都有關系。鋁件加工表面應光潔、平正、鑄字標志應清晰,澆、冒口清理后與鑄件表面應齊平。 消防鋁配件對于邊蓋類薄壁零件,采用鈑金冷做校正;容易磨損的軸孔類零件可采用金屬噴鍍、焊修、膠粘、機械加工等工藝以達到原廠尺寸。